Flow Research
has completed a new set of three market studies on the
worldwide ultrasonic flowmeter market.
These studies determined the size of the ultrasonic flowmeter market
in 2022 with input for 2023 and forecast its market size through 2027.
This was our first look at the ultrasonic flowmeter market since the
pandemic. The three studies are called:
-
Core Study: The World Market for
Ultrasonic Flowmeters, 7th Edition
-
·Module A: The World Market
for Inline Ultrasonic Flowmeters
-
·Module B: The
World Market for Clamp-on and Insertion Ultrasonic Flowmeters
See the
forest and the trees with our three studies:
This is the 7th Edition of this study, which was previously published in
2001, 2003, 2008, 2012, 2017, and 2021. This study series includes three
components that, together, cover the entire scope of the ultrasonic
flowmeter market but can also function as standalones. The new studies
build on the knowledge gained over the years since our last full treatment
of the subject but will also represent a completely fresh look at the
market.
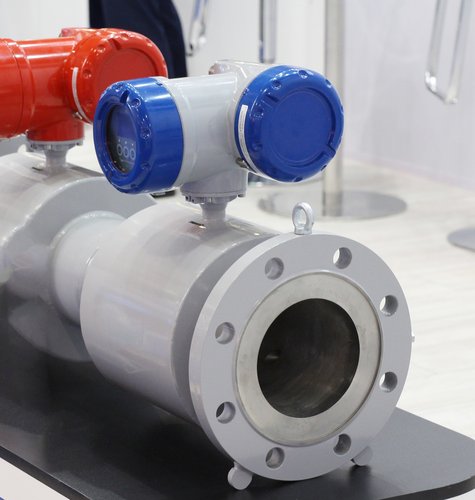
Creating
three separate modules for the ultrasonic study has proved to be very
enlightening. For example,
multipath inline ultrasonic flowmeters are especially important in the
fast-growing market for custody transfer of natural gas.
This ultrasonic technology type is highlighted here in Module
A, and it is analyzed in terms of dollar and unit shipments
worldwide and by region, as well as by average selling prices worldwide and
by region.
Core Study
The Core
Study of the Ultrasonic series analyzes the world market for all types of
ultrasonic flowmeters. It will include 2022 market size with reliable input
for 2023, provides
in-depth segmentation of the market by various product and geographic
categories, provides detailed market growth projections through 2027, and
includes 2022 market shares. It also includes a technology analysis,
profiles of significant supplier companies, and provides detailed market
strategies for suppliers. The studies gauge the extent of the
post-pandemic rebound that is boosting many markets.
Module A –
Inline
The inline market is quite different from the clamp-on and
insertion markets. This applies
to applications, industries, price points, and many other factors.
By isolating the inline (spoolpiece) market from the clamp-on and
insertion markets, a much more compelling and informative analysis results
This
study, Module A of the ultrasonic series, analyzes the world market
for inline ultrasonic flowmeters.
It includes a technology analysis, 2022 and 2023 market size data,
and provides in-depth segmentation of the market by various product and
geographic categories. It also
includes detailed market growth projections through 2027 for all types of
inline ultrasonic flowmeters. Detailed
market strategies are provided for suppliers.
Module B – Clamp-on and Insertion
This study, Module B of the
ultrasonic series, analyzes the world markets for clamp-on and for insertion ultrasonic flowmeters, with a
dedicated chapter for each. This
study covers 2022 and 2023 market size with detailed segmentation and
forecasts through 2027. It
includes technology analysis, 2019 market shares of major suppliers,
average selling prices, supplier profiles, product analyses, and
discussions of market circumstances and growth factors.
Detailed market strategies are provided for suppliers.
Module B: The World
Market for Clamp-On and Insertion Ultrasonic Flowmeters,
contains its own set of segmentation
designed to provide a comprehensive view of these two members of ultrasonic
flowmeter technology and its markets. There
is segmentation to address the unique qualities of these two ultrasonic
flowmeter designs. The study
segmentation specific to clamp-on and to insertion design types in the
Study Overview.
Clamp-on
and insertion ultrasonic flowmeters have established their own set of
advantages within the flow measurement market.
Clamp-on devices are highly versatile in that they can be installed
in either a portable or fixed manner, making them ideal choices for
economical meter upgrades, as check meters, and a host of other
applications. Clamp-on
ultrasonic flowmeters are suitable for use with gas, liquid, and steam
flows. Insertion devices permit
users to obtain the benefits of ultrasonic technology in virtually any line
size.
Modules
A and B Together
The two
modules analyze the inline, clamp-on, and insertion markets individually,
enabling us to separate out unit price and unit quantity data for each
technology, and to provide a distinctive analysis for each of these three
fundamentally different ultrasonic flowmeter types.
Together these three studies enable you to see both the forest
and the trees when it comes to the ultrasonic flowmeter market. Flow
Research stands alone in providing such a comprehensive analysis of the
worldwide ultrasonic flowmeter market.
Ultrasonic Flowmeter History
Tokyo
Keiki had first introduced ultrasonic clamp-on flowmeters to commercial
markets in Japan in 1963. In
1971, Badger Meter first brought clamp-on ultrasonic flowmeters to the
United States by reselling Tokyo Keiki’s meters. In 1972, Controlotron
began manufacturing its clamp-on ultrasonic flowmeters in Long Island, New
York. In the late 1970s and
early 1980s, Doppler flowmeters began to be used.
Because they were not well understood, they were often misapplied.
As a result, many users got a bad impression of ultrasonic
flowmeters during this time. In
the 1990s, transit-time emerged as the leading ultrasonic technology, and
ultrasonic meters began growing significantly in popularity and
capabilities.
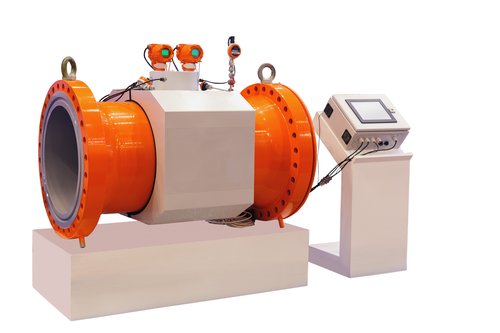
In
the early 1980s, both Panametrics and Ultraflux experimented with
ultrasonic meters for gas-flow measurement. In the mid-1990s, a group
called Group Europeen de Recherches Gaziers (GERG) published a technical
monograph on ultrasonic flowmeters for gas flow measurement. A monograph
out of GERG led to increased European ultrasonic flowmeter use from 1996 to
1999.
The
GERG monograph laid the groundwork for the publication of AGA-9 by the
American Gas Association. AGA-9 lays out criteria for using ultrasonic
flowmeters for custody-transfer applications. Since its publication in June
1998, ultrasonic flowmeters have become widely used for custody transfer of
natural gas. They are especially suited for measuring gas flow in large
pipelines, easily handling flow in those above 20 inches in diameter, as
well as smaller pipelines. Its main competitors for custody transfer of
natural gas are the differential-pressure (DP) orifice meter and turbine
flowmeter.
It
used to be standard practice to divide the ultrasonic flowmeter market up
according to whether the meters are transit-time, Doppler or hybrid.
Traditional use of transit-time meters was to clean liquids, while Doppler
meters handle fluids with impurities. Hybrid meters are a combination of
transit-time and Doppler, and use one technology or the other, depending on
the fluid. In the past 10 years, transit-time suppliers made great progress
getting transit-time meters to measure fluid flows with some impurities. As
a result, Doppler and hybrid meters are less important since transit-time
meters are now used for applications previously reserved for Doppler
meters. Another reason for growth in transit-time meters is their use in
energy industries, mainly oil and gas, within which Doppler flowmeters play
no major role.
Mounting
type is now the more useful way to classify ultrasonic flowmeters, rather
than transit time vs. Doppler. Three main mounting types for ultrasonic
flowmeters include:
-
·
Inline
-
·
Clamp-on
-
·
Insertion
Inline
ultrasonic flowmeters are mounted with a meter body in the pipe. Inline
meters achieve the highest accuracy of any ultrasonic meters, and multipath
ultrasonic meters are inline meters. Multipath meters have three or more
ultrasonic signals or “paths” to determine flow velocity. This gives
them greater accuracy than single- and dual-path meters. The most common
number of paths is four, five and six, but some multi-path meters have
eight, 12 or even 18 paths. Inline meters are used for custody transfer
applications.
Clamp-on
meter disadvantages limit their usefulness in certain situations. The
ultrasonic signal can be attenuated by the pipe wall. Knowing pipe-wall
thickness and composition can be important. In addition, build-up on the
inside of the pipe wall can affect the internal diameter of the pipe.
Knowing the internal pipe diameter is important to getting a correct
flowmeter reading.
Insertion
meters are sometimes used in large pipes when a spool-piece would be
expensive. They have a cost-advantage over inline meters since there is no
meter body. Insertion meters go into a hole drilled in the pipe wall. They
are widely used in stack-gas and exhaust-flow monitoring. Here they compete
with DP flowmeters using averaging Pitot tubes and with thermal flowmeters.
Background of technology
Ultrasonic
flowmeters have been gaining acceptance over the last decade as end-users
come to understand and appreciate the technology -- although some are just
now discovering the advantages and potential of ultrasonic flow
measurement.
The
ultrasonic flowmeter market is still a relatively new technology. Tokyo
Keiki first introduced ultrasonic flowmeters to commercial markets in Japan
in 1963. In 1972, Controlotron introduced the first clamp-on ultrasonic
flowmeter to the United States. In the late 1970s and early 1980s, Doppler
flowmeters began to be used.
Because
ultrasonic flowmeters were not well understood at first, they were often
misapplied. As a result, many users got a bad impression of the meters
during this time. It was not until the 1990s that ultrasonic flowmeters
began to be widely used for industrial applications.
The rapidly
expanding market for gas flow measurement is one of the major reasons for
strong projected growth in the ultrasonic flowmeter market. Energy,
including energy conservation, and other markets have the potential to
create even more demand, particularly as the technology improves to enable
new applications.
Advantages
Ultrasonic
flowmeters feature high accuracy, high reliability, high turndown ratios,
long service life, low maintenance, relatively low cost, valuable
diagnostics, no moving parts, and redundancy capabilities. Clamp-on
ultrasonic flowmeters, in particular, can offer redundancy by providing an
easy check of an inline meter. In addition to the traditional
advantages, suppliers are significantly improving accuracy, sensitivity,
and reliability.
Ultrasonic
flowmeters have a distinct advantage over other flowmeters:
-
Unlike Coriolis meters, ultrasonic flowmeters
do very well in large pipe sizes.
-
In large-size, natural gas pipeline
applications, ultrasonic flowmeters have the advantage over turbine and
differential pressure (DP) flowmeters of being highly accurate,
non-intrusive, and highly reliable over time, with no moving parts to
wear. They also have an advantage over DP flowmeters in that they are
largely non-intrusive, with the exception of insertion types.
-
Ultrasonic
flowmeters have an advantage over magnetic flowmeters in that they can
be used to measure the flow of nonconductive liquids, gases, and steam.
-
Ultrasonic flowmeters have an advantage over
vortex flowmeters in that they can meter low flows better than vortex
meters.
Further
sweetening the pot is the fact that average ultrasonic prices are holding
their own or even declining. In comparison, the average price for Coriolis
flowmeters has had upward pressure due to introductions of large-line size
models in the 12" - 16" diameter range.
A range of
applications
Ultrasonic
flowmeters are used in upstream applications for allocation metering, for
measuring gas and oil from test and production separators, for check
metering, and for other applications. A major use of ultrasonic flowmeters
is in the midstream segment for custody transfer of natural gas.
Multipath ultrasonic flowmeters achieve very high accuracy in measuring
both liquids and gases.
Probably
the single most important factor in the recent growth of ultrasonic
flowmeters in the past 25 years has been the rapid growth in the market for
multipath ultrasonic meters for custody transfer of natural gas. Multipath
ultrasonic meters have three or more paths. The benefit of having multiple
paths is that flow is measured at more points in the flowstream. This
enhances the accuracy of the measurement. In 1998, the
American Gas Association (AGA) approved the use of ultrasonic flowmeters
for custody transfer applications. Since that time, suppliers have
researched multipath meters and brought out new products.
Ultrasonic
flowmeters are also being more widely used to measure process gas and flare
gas. Insertion meters are used to measure flare gas in stacks, and
ultrasonic flowmete rs are used
more widely in the chemical and refining industries.
In other
areas, the increased use of battery power supplies opens up additional
opportunities for ultrasonic flowmeters in the water and irrigation
industries as well as other applications. Battery powered flowmeters offer
low energy consumption independent of the main power grid and can help
reduce prices on the worldwide market.
How they work
There are two
main types of ultrasonic flowmeters:
A transit
time ultrasonic flowmeters has both a sender and a receiver. It
sends two ultrasonic signals across a pipe at an angle: one with the flow,
and one against the flow. The meter then measures the “transit
time” of each signal. When the ultrasonic signal travels with
the flow, it travels faster than when it travels against the flow. The
difference between the two transit times is proportional to flowrate.
Transit time
ultrasonic flowmeters are distinguished according to the number of
“paths” they have. A path is simply the path or track of the ultrasonic
pulse as it travels across the pipe and back again. Many ultrasonic
flowmeters are single or dual path, meaning that they send either one or
two signals across a pipe and back. Typically, there are two transducers
for each path; one is a sender and one is a receiver.
Doppler
flowmeters also send an ultrasonic signal
across a pipe. Instead of tracking the time the signal takes to cross
to the other side, a Doppler flowmeter relies on having the signal
deflected by particles in the flowstream. These particles are
traveling at the same speed as the flow. As the signal passes through the
stream, its frequency shifts in proportion to the mean velocity of the
fluid. A receiver detects the reflected signal and measures its frequency.
The meter calculates flow by comparing the generated and detected
frequencies. Doppler ultrasonic flowmeters are used with dirty liquids or
slurries. They are not used to measure gas flow.
Articles
about Ultrasonic Flowmeters
Previous
Studies:
The
World Market for Ultrasonic Flowmeters, 6th Edition
Published
2021
The
World Market for Ultrasonic Flowmeters, 5th Edition
Published
2017
The
World Market for Ultrasonic Flowmeters, 4th Edition
Published
2012
The World Market for Ultrasonic Flowmeters, 3rd Edition
Published
2008
The World Market for Ultrasonic Flowmeters, 2nd Edition (2003) Provides historical perspective
The World Market for Ultrasonic Flowmeters, 1st Edition (2001)
Provides historical perspective
|